Variable speed drive for ID Fan of power plant
Technology of medium voltage variable frequency speed adjustment is a new type driving technology which emerged in 1990s. It is mainly used for AC motor speed adjustment. Its technology and performance are superior to any other speed adjustment mode (such as voltage drop adjustment, pole-changing control, slip difference control, cascaded control and hydraulic coupling). Variable frequency adjustment is accepted by most users as its evident energy saving, high precision, wide adjustment range, completed protections and auto communication. It also brings most convenient and fastest service in terms of reliable operation, easy installation and free maintenance. It has been first choice product of energy saving.
A Power Plant is 500MW steam turbine generator. Boilers of two generators are equipped with two ID fans which are all axis flow fans. Air flow is controlled by damper. During operation, max opening of damper is not more than 85%. The adjustment just changes flow resistance. Output power does not change. Throttle loss is big and much power is wasted. In the mean time, during starting of motor, it creates impact current which is 5~7 times of rated current. Automatization level of ID fan is low. Adjustment is not timely and operation efficiency is low. Thereby, plant decides to reconstruct with variable frequency adjustment to reduce flooding loss and throttle loss.
I. Constitution of medium voltage variable frequency speed adjustment system
1. Characters of ID fan
Air flow needs to vary with load variety. Because model of fan was selected in early term, air flow is adjusted just by damper opening, which causes much energy wasted. In the mean time, generator does not cooperate with DCS well due to slow response and non-linearity. Automatization level lowers greatly.
2. Variable frequency speed adjustment system of boiler
Four variable speed drives adopt scheme of "one drive one".
Parameters of Variable Speed Drive
3. Characters of variable frequency speed adjustment system
Personnel adjusts output value of DCS according to temperature of flue gas, temperature of boiler vapour and negative pressure. This output value is given value of frequency (speed) which is 4~20mA signal feeding back to variable speed drive. Variable speed drive compares speed output and given value, then adjusts motor speed automatically.
On above base, draw curve of given value in different loads and temperatures. Fix safe up limitation and safe low limitation, make special arithmetic of fan speed adjustment. Send samples of load, temperature and negative pressure variety to DCS. DCS makes control operation, feeds back the outcome to variable speed drive in form of 4~20mA signal. variable speed drive adjusts speed automatically through comparing speed output and given value from DCS, thereby adjusting motor speed and implementing auto control of fan speed.
Here are characters of variable frequency speed adjustment system: speed adjustment system can run in variable frequency, and also can switch to direct on line. When control power of variable speed drive is off, inside UPS can supply power to maintain continuous operation. When speed given from DCS faults, variable speed drive alarms, meanwhile, variable speed drive continues to run in original speed and keeps working condition unchangeable. Preserve original motor, no need to change original equipment.
II. Energy saving analysis
1. Parameters
2. Fan parameters in each load
3. Calculation
Power calculation in direct on line state
During operation, fan A and fan B should be adjusted simultaneously according to load variety. Performance indexes of fan A and fan B are same. So we make consolidation of data of A and B. Infer power consumption in variable frequency state according to curve of flow percentage and damper opening.
Pd: motor power;U: input voltage of motor;I: input current of motor;COSφ: power factor.
Formula: Pd=1.732×U×I×COSφ
We can calculate COSφ according to above formula.
Get following table after processing ID fan data
We get following linearity relation of damper opening and total power according to above data.
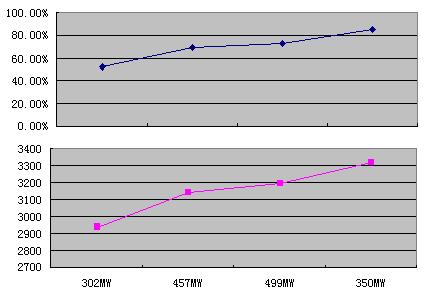
Note: Blue line: damper opening; Pink line: total power
We infer total power at 100% opening:
P100=(3192.30-3142.54)/(73.1-69.5)×(100-73.1)+3192.73=3935.89kW
That is, total power is 3935.89kW when opening is 100%
Power calculation in variable frequency state
Fan is square torque load. Its speed N, flow Q, pressure H and shaft power P have following relations: Q∝N,H∝N2,P∝N3
That is, flow is in direct rate to speed. Pressure is in direct rate to square of speed. Shaft power is in direct rate to cube of speed. As per formula: P//Pdn=( N // N0)3=(Q//Q0)3, we can calculate total power consumption in each load.
Pdn is power of 100% opening, equal to P100.
For load of fan, opening rate is regarded as air flow rate approximately.
Energy saving rate:
л= (Pd- Pb)/ Pd×100%
we get following result according to above formula
III. Conclusion
How to lower cost, heighten competitive power, strengthen management and explore energy saving is an important event that power plant must research. Making reconstruction with medium voltage variable frequency speed adjustment for equipments, such as ID fan, FD fan, feed pump and circulating pump, not only lowers power consumption and coal consumption, but also heightens safety and reliability, reduces system faults.
A Power Plant is 500MW steam turbine generator. Boilers of two generators are equipped with two ID fans which are all axis flow fans. Air flow is controlled by damper. During operation, max opening of damper is not more than 85%. The adjustment just changes flow resistance. Output power does not change. Throttle loss is big and much power is wasted. In the mean time, during starting of motor, it creates impact current which is 5~7 times of rated current. Automatization level of ID fan is low. Adjustment is not timely and operation efficiency is low. Thereby, plant decides to reconstruct with variable frequency adjustment to reduce flooding loss and throttle loss.
I. Constitution of medium voltage variable frequency speed adjustment system
1. Characters of ID fan
Air flow needs to vary with load variety. Because model of fan was selected in early term, air flow is adjusted just by damper opening, which causes much energy wasted. In the mean time, generator does not cooperate with DCS well due to slow response and non-linearity. Automatization level lowers greatly.
2. Variable frequency speed adjustment system of boiler
Four variable speed drives adopt scheme of "one drive one".
Parameters of Variable Speed Drive
Capacity (kVA) | 2250 | Analogue input | 0~10V/4~20mA |
Matching motor power (kW) | 2200 | Analogue output | 0~10V/4~20mA |
Rated output current (A) | 220 | Accelerating/decelerating time | 0.1~3000s |
Input frequency (Hz) | 45~55 | Digital output/input | Extended according to user demand |
Rated input voltage (V) | 6000V±10% | Ambience temperature | 0~40degree |
Power factor | 0.95 (>20% load) | Storage/transportation temperature | -40~70 degree |
Efficiency | >0.96 | cooling | Air cooling |
Output frequency (Hz) | 0~120 | Humidity | <90%, without condensation |
Resolution (Hz) | 0.01 | Altitude | <1000m |
Over load | 120%1min, 150%3s, 200%immediately | IP | IP20 |
3. Characters of variable frequency speed adjustment system
Personnel adjusts output value of DCS according to temperature of flue gas, temperature of boiler vapour and negative pressure. This output value is given value of frequency (speed) which is 4~20mA signal feeding back to variable speed drive. Variable speed drive compares speed output and given value, then adjusts motor speed automatically.
On above base, draw curve of given value in different loads and temperatures. Fix safe up limitation and safe low limitation, make special arithmetic of fan speed adjustment. Send samples of load, temperature and negative pressure variety to DCS. DCS makes control operation, feeds back the outcome to variable speed drive in form of 4~20mA signal. variable speed drive adjusts speed automatically through comparing speed output and given value from DCS, thereby adjusting motor speed and implementing auto control of fan speed.
Here are characters of variable frequency speed adjustment system: speed adjustment system can run in variable frequency, and also can switch to direct on line. When control power of variable speed drive is off, inside UPS can supply power to maintain continuous operation. When speed given from DCS faults, variable speed drive alarms, meanwhile, variable speed drive continues to run in original speed and keeps working condition unchangeable. Preserve original motor, no need to change original equipment.
II. Energy saving analysis
1. Parameters
Equipment | ID fan |
Fan model | ARB4500-2A/90 |
Flow (105Nm3/h) | 20.376 |
Full pressure (pa) | 1256 |
Motor model | YKK2200-16 |
Motor power Pdn (kW) | 2200 |
Motor speed N0(r/min) | 372 |
Motor voltage U0 (kV) | 6 |
Motor current I0 (A) | 292 |
Power factor of motor | 0.84 |
2. Fan parameters in each load
ID fan | Load (MW) | 302 | 350 | 457 | 499 |
A | Opening (%) | 53 | 85 | 69.7 | 74 |
Motor current (A) | 168.5 | 191 | 182.4 | 185.7 | |
B | Opening (%) | 52 | 85 | 69.3 | 72.2 |
Motor current (A) | 168.2 | 189 | 177.6 | 180 |
3. Calculation
Power calculation in direct on line state
During operation, fan A and fan B should be adjusted simultaneously according to load variety. Performance indexes of fan A and fan B are same. So we make consolidation of data of A and B. Infer power consumption in variable frequency state according to curve of flow percentage and damper opening.
Pd: motor power;U: input voltage of motor;I: input current of motor;COSφ: power factor.
Formula: Pd=1.732×U×I×COSφ
We can calculate COSφ according to above formula.
Get following table after processing ID fan data
Load (MW) | 302 | 350 | 457 | 499 |
Average opening (%) | 52.5 | 85 | 69.5 | 73.1 |
Motor current (A) | 336.7 | 380 | 360 | 365.7 |
Total power (kW) | 2939.15 | 3317.13 | 3142.54 | 3192.30 |
We get following linearity relation of damper opening and total power according to above data.
Note: Blue line: damper opening; Pink line: total power
We infer total power at 100% opening:
P100=(3192.30-3142.54)/(73.1-69.5)×(100-73.1)+3192.73=3935.89kW
That is, total power is 3935.89kW when opening is 100%
Power calculation in variable frequency state
Fan is square torque load. Its speed N, flow Q, pressure H and shaft power P have following relations: Q∝N,H∝N2,P∝N3
That is, flow is in direct rate to speed. Pressure is in direct rate to square of speed. Shaft power is in direct rate to cube of speed. As per formula: P//Pdn=( N // N0)3=(Q//Q0)3, we can calculate total power consumption in each load.
Pdn is power of 100% opening, equal to P100.
For load of fan, opening rate is regarded as air flow rate approximately.
Energy saving rate:
л= (Pd- Pb)/ Pd×100%
we get following result according to above formula
Load (MW) | 302 | 350 | 457 | 499 |
Average opening (%) | 52.5 | 85 | 69.5 | 73.1 |
Total power in variable frequency (kW) | 569.5351 | 2417.127 | 1321.287 | 1537.428 |
Energy saving rate (%) | 80.62 | 27.13 | 57.95 | 51.84 |
III. Conclusion
How to lower cost, heighten competitive power, strengthen management and explore energy saving is an important event that power plant must research. Making reconstruction with medium voltage variable frequency speed adjustment for equipments, such as ID fan, FD fan, feed pump and circulating pump, not only lowers power consumption and coal consumption, but also heightens safety and reliability, reduces system faults.
<- - I have an Opinion - ->