Variable speed drive for dusting fan in Steel & Iron industry
There is 1# and 2# metal mixer in a Steel & Iron Group. Every mental mixer has a slag tap and a tap hole. During adding iron or iron output, melting iron reacts with air intensively, creating much flue gas. It is harmful to workers and also pollutes environment. In order to improve environment and lower pollution, dusting system is necessary. Steel plant installs a dusting fan. The fan needs five air flows to adapt technics need. Fan speed should be controlled in order to heighten fan efficiency and save energy. In original projects, hydraulic coupling used to be adopted. With rapid development of high voltage variable frequency technology, hydraulic coupling is losing its advantage gradually. The variable speed drive was selected eventually. The variable speed drive put into service in April, 2003. It has been running stably for a year.
Technics requirements of dusting fan
There is 1# mixer and 2# mixer in steel plant. Air flow is not needed when there is no iron input or output. During working of mixer, slag tap needs air flow 350000m3/h;tap hole needs 150000m3/h. 300000m3/h air flow is needed when tap holes of two mixer output iron simultaneously. 500000m3/h is needed when slag tap and tap hole of one mixer work simultaneously. Slag taps of two mixers can not open simultaneously. Tap holes of two mixers can open simultaneously.
Adding iron: by crane of 125t. Melting iron jar has two models : 70t and 100t. Adding period of each jar is 4~6min.
Outputting iron: calculate as per: three converters produce 20 furnaces/shift, single mix outputs iron 30jars/shift. Three shifts a day and 8 hours a shift. Single jar output time: 1~2min. Shortest period of output is 8min. Accumulative time of output of each shift: 30~60min.
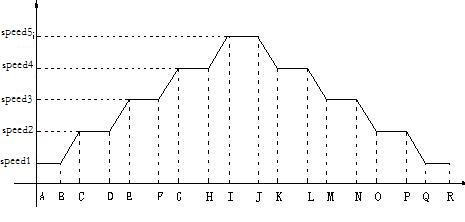
A~B: both slag tap and tap hole do not work
B~D: work time of tap hole. B~C: fan acceleration time
D~F: work time of two tap holes. D~E: fan acceleration time
F~H: work time of one slag tap. F~G: fan acceleration time
H~J: work time of slag tap and tap hole. H~I: fan acceleration time. During acceleration, it can skip any acceleration point according to need.
J: fan begins to decelerate.
J~L: time of one slag tap work and one tap hole work transferring to one slag tap work. J~K: fan deceleration time
L~N: time of one slag tap work transferring to two tap holes work. L~M: fan deceleration time.
N~P: time of two tap holes work transferring to one tap hole work. N~O: fan deceleration time.
P~R: time of one tap hole work transferring to no iron adding or output. P~Q: fan deceleration time.
Q~R: both slag tap and tap hole do not work
Requirements of speed adjustment
Unit : m3/h
Variable speed drive sets speeds of 5 stages according to above table and speeds are required to be adjusted. Lowest speed of fan is set 10Hz temporarily and it is variable speed drive acceleration time is 46s (0~50Hz), no requirement for deceleration time. Variable speed drive should meet requirement of accelerating during deceleration.
Metal mixer of the steel plant uses a variable speed drive to control speed. The variable speed drive is high-high voltage source drive. Its main data is following: capacity is 1050KVA, rated output current is 105A, input frequency 45Hz~55Hz, rated input voltage 6000V, allowable voltage vibration -10%~10%, input power factor ≥0.96, output frequency 0~50Hz (speed adjustment range 0~100%), variable speed drive efficiency ≥98% (not including transformer), frequency resolution is 0.01Hz, stepless speed adjustment, overload capacity: 120% for 1min and 150% immediately. Acceleration time and deceleration time are set as per technics requirement.
Energy saving calculation
1. Principle of energy saving
variable speed drive can accelerate /decelerate motor speed according to technics need, change curve of fan, make fan parameter meet requirement of technics. There is following relationship between flow, pressure, power and speed:
Q1/Q2=n1/n2
H1/H2=(n1/n2)2
P1/P2=(n1/n2)3
Q1, H1, P1—flow, pressure and power when pump runs at speed n1
Q2, H2, P2—flow, pressure and power when pump runs at speed n2
If speed lowers a half, namely n2/n1=1/2,so P2/P1=1/8, we see speed reduction can lower shaft power to save energy.
In variable speed drive control, power factor is near to 1 at full load 50Hz. Operation current is far less than rated current. Reason is that filter capacitors inside variable speed drive take effect in improving power factor, saving 20% capacity for power grid.
2. Operation record
PLC inside variable speed drive and HMI bring convenient for commissioning. Commissioning period shortens a lot. Setting all parameters is very easy. Adjust air flow of each stage in time according to flue gas quantity. After reforming with variable speed drive, environment is improved greatly.
3. Energy Saving
Statistic daily operation time in each stage, we get following data:
variable speed drive input power of each speed stage:
P1=1.732×6×5.8×0.8=48.2kW
P2=1.732×6×25.1×0.8=208.7kW
P3=1.732×6×37.9×0.8=315.1kW
P4=1.732×6×23.89×0.8=198.6kW
P5=1.732×6×62.50×0.8=519.6kW
Daily power consumption of fan:
48.2×3+208.7×7+315.1×4+198.6×7+519.6×3=4694.9 kW·h
Power price: 0.4yuan, yearly work time: 300days, yearly power cost:
4694.9×0.4×300=563388yuan
In direct on line state, yearly power cost:
P=1.732×6×76×0.8=631.8kW
631.8×24×300×0.4=1820000yuan
Cost saved: 1257000yuan (USD 184852)
Other benefits of variable speed drive application
Problem of resisting disturbance. variable speed drive is controlled by system PLC. There are 4 routes analogue output. 2 routes enter into instrument of controller cabinet to display. 2 routes enter into PLC to involve protections. During commissioning, signal entering into instrument is fine, but signal entering into system PLC is sporadic. After detecting, PLC analogue signal is normal. Later on, we solve the problem by earthing system PLC reliably.
Inrush current problem of dry transformer. The variable speed drive adopts technology of cell-cascade multi-level, with a dry transformer. In this project, transformer is epoxy casting transformer with F class insulation. As per transformer manual, inrush current should be within 6 magnification. Set instantaneous protection of high voltage breaker as 7. Supplying power to variable speed drive is sporadic. Power can not be supplied to variable speed drive sometimes due to instantaneous protection activity of breaker. Later on, problem is solved by increasing instantaneous protection value to 11 from 7.
Technics requirements of dusting fan
There is 1# mixer and 2# mixer in steel plant. Air flow is not needed when there is no iron input or output. During working of mixer, slag tap needs air flow 350000m3/h;tap hole needs 150000m3/h. 300000m3/h air flow is needed when tap holes of two mixer output iron simultaneously. 500000m3/h is needed when slag tap and tap hole of one mixer work simultaneously. Slag taps of two mixers can not open simultaneously. Tap holes of two mixers can open simultaneously.
Adding iron: by crane of 125t. Melting iron jar has two models : 70t and 100t. Adding period of each jar is 4~6min.
Outputting iron: calculate as per: three converters produce 20 furnaces/shift, single mix outputs iron 30jars/shift. Three shifts a day and 8 hours a shift. Single jar output time: 1~2min. Shortest period of output is 8min. Accumulative time of output of each shift: 30~60min.
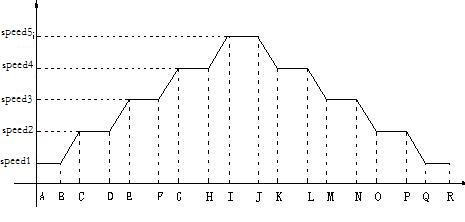
A~B: both slag tap and tap hole do not work
B~D: work time of tap hole. B~C: fan acceleration time
D~F: work time of two tap holes. D~E: fan acceleration time
F~H: work time of one slag tap. F~G: fan acceleration time
H~J: work time of slag tap and tap hole. H~I: fan acceleration time. During acceleration, it can skip any acceleration point according to need.
J: fan begins to decelerate.
J~L: time of one slag tap work and one tap hole work transferring to one slag tap work. J~K: fan deceleration time
L~N: time of one slag tap work transferring to two tap holes work. L~M: fan deceleration time.
N~P: time of two tap holes work transferring to one tap hole work. N~O: fan deceleration time.
P~R: time of one tap hole work transferring to no iron adding or output. P~Q: fan deceleration time.
Q~R: both slag tap and tap hole do not work
Requirements of speed adjustment
Unit : m3/h
SR | Item | Mode 1 | Mode 2 | Mode 3 | Mode 4 | Mode 5 | Mode 6 | Mode 7 | Mode 8 |
1 | 1# tap hole valve | 150000 |
|
|
|
150000 | 150000 |
|
|
2 | 1# slag tap valve |
|
350000 |
|
|
|
|
350000 |
|
3 | 2# tap hole valve |
|
|
150000 |
|
150000 |
|
150000 |
|
4 | 2# slag tap valve |
|
|
|
350000 |
|
350000 |
|
|
5 | Total air flow | 150000 | 350000 | 150000 | 350000 | 300000 | 500000 | 500000 | 0 |
6 | Speed adjustment rate | 300000 | 700000 | 300000 | 700000 | 600000 | 1000000 | 1000000 | 20 |
Variable speed drive sets speeds of 5 stages according to above table and speeds are required to be adjusted. Lowest speed of fan is set 10Hz temporarily and it is variable speed drive acceleration time is 46s (0~50Hz), no requirement for deceleration time. Variable speed drive should meet requirement of accelerating during deceleration.
Metal mixer of the steel plant uses a variable speed drive to control speed. The variable speed drive is high-high voltage source drive. Its main data is following: capacity is 1050KVA, rated output current is 105A, input frequency 45Hz~55Hz, rated input voltage 6000V, allowable voltage vibration -10%~10%, input power factor ≥0.96, output frequency 0~50Hz (speed adjustment range 0~100%), variable speed drive efficiency ≥98% (not including transformer), frequency resolution is 0.01Hz, stepless speed adjustment, overload capacity: 120% for 1min and 150% immediately. Acceleration time and deceleration time are set as per technics requirement.
Energy saving calculation
1. Principle of energy saving
variable speed drive can accelerate /decelerate motor speed according to technics need, change curve of fan, make fan parameter meet requirement of technics. There is following relationship between flow, pressure, power and speed:
Q1/Q2=n1/n2
H1/H2=(n1/n2)2
P1/P2=(n1/n2)3
Q1, H1, P1—flow, pressure and power when pump runs at speed n1
Q2, H2, P2—flow, pressure and power when pump runs at speed n2
If speed lowers a half, namely n2/n1=1/2,so P2/P1=1/8, we see speed reduction can lower shaft power to save energy.
In variable speed drive control, power factor is near to 1 at full load 50Hz. Operation current is far less than rated current. Reason is that filter capacitors inside variable speed drive take effect in improving power factor, saving 20% capacity for power grid.
2. Operation record
Speed point | Motor speed | variable speed drive frequency | Input current A | Output current A | Operation time (h) | Operation state |
1 | 240round/min | 20Hz | 5.80 | 40.09 | 3 | No iron adding or outputting |
2 | 420 round/min | 35 Hz | 25.10 | 50.79 | 7 | One tap hole outputs iron |
3 | 480 round/min | 40 Hz | 37.90 | 58.20 | 4 | Two tap holes output iron |
4 | 410 round/min | 34.2Hz | 23.89 | 49.50 | 7 | One slag tap adds iron |
5 | 600 round/min | 50 Hz | 62.50 | 76.00 | 3 | One mixer adds iron and the other outputs iron |
PLC inside variable speed drive and HMI bring convenient for commissioning. Commissioning period shortens a lot. Setting all parameters is very easy. Adjust air flow of each stage in time according to flue gas quantity. After reforming with variable speed drive, environment is improved greatly.
3. Energy Saving
Statistic daily operation time in each stage, we get following data:
variable speed drive input power of each speed stage:
P1=1.732×6×5.8×0.8=48.2kW
P2=1.732×6×25.1×0.8=208.7kW
P3=1.732×6×37.9×0.8=315.1kW
P4=1.732×6×23.89×0.8=198.6kW
P5=1.732×6×62.50×0.8=519.6kW
Daily power consumption of fan:
48.2×3+208.7×7+315.1×4+198.6×7+519.6×3=4694.9 kW·h
Power price: 0.4yuan, yearly work time: 300days, yearly power cost:
4694.9×0.4×300=563388yuan
In direct on line state, yearly power cost:
P=1.732×6×76×0.8=631.8kW
631.8×24×300×0.4=1820000yuan
Cost saved: 1257000yuan (USD 184852)
Other benefits of variable speed drive application
- Technics is improved. In variable speed drive control, dusting fan can adjust air flow smoothly. Operation personnel can adjust parameters easily.
- Lifetime of fan and motor is prolonged. Dusting fan is usually centrifugal fan. Its start-up time is long and start current is big (6~8 times of rated current), which brings big impact on motor and fan. In variable speed drive control, soft start and soft stop cause little impact, which prolongs lifetime of machine.
- Wear and tear of valve and impeller is reduced. In variable speed drive control, fan usually runs at speed which lowers 150 round/min than rated speed. So wear and tear of impeller, motor and bearing is much reduced. It prolongs maintenance interval of fan and saves maintenance cost.
- Automatization is easy. Air flow of dusting system changes as per technics requirement. In damper control, there is linearity problem of opening angle and flow relationship. Because of serious wear and tear, valve character changes, causing non-linearity problem, thereby leading to incorrect adjustment and abnormal work of control system. In technology of variable frequency, it keeps linearity in high precision 0.1~0.01Hz all the time, which creates favorable conditions for automatization.
Problem of resisting disturbance. variable speed drive is controlled by system PLC. There are 4 routes analogue output. 2 routes enter into instrument of controller cabinet to display. 2 routes enter into PLC to involve protections. During commissioning, signal entering into instrument is fine, but signal entering into system PLC is sporadic. After detecting, PLC analogue signal is normal. Later on, we solve the problem by earthing system PLC reliably.
Inrush current problem of dry transformer. The variable speed drive adopts technology of cell-cascade multi-level, with a dry transformer. In this project, transformer is epoxy casting transformer with F class insulation. As per transformer manual, inrush current should be within 6 magnification. Set instantaneous protection of high voltage breaker as 7. Supplying power to variable speed drive is sporadic. Power can not be supplied to variable speed drive sometimes due to instantaneous protection activity of breaker. Later on, problem is solved by increasing instantaneous protection value to 11 from 7.
<- - I have an Opinion - ->