Variable speed drive for Cycling Pumps
The total installed capacity of the Power Generation is 4×300MW. Each generator unit is provided with two cycling pumps. And the outlet valves of the pumps uses butterfly valves, which have two positions only, full open and full close. The flow of cooling water is adjusted through the number of operating pumps. Because of the temperature difference with seasons as well as day and night, it is often happened that the flow for one pump is not enough and the flow for two pumps is too high. Since this primitive adjustment method, the vacuum of the turbines is not stable and economic operation of the turbines cannot be ensured. Meanwhile, a large quantity of electric energy and water resources are wasted, leading to the high power consumption, huge consumed coal quantity and the power generating costs cannot be reduced. So it is critical to select a suitable speed adjusting method to make reform to the cycling pumps. Therefore, the company decided to use the variable speed drive of 6kV/ 1800W for the cycling pump for generator unit #1.
Features of Operating Mode of Cycling Pumps
Closed cycling water systems are used for the generator unit and water supply systems of unit system are used for the cycling pumps, i.e. each generator is provided with one cooling tower, one pressure cycling water pipe, one gole with double holes and two cycling pumps, and under normal operating mode, two cycling pumps are operated for each generator unit. In the cycling water systems, cycle utilization of water resources is implemented by using the cycling pump. The hot water passes the heat exchanger and enters into the cooling facilities to cool down, reducing the water temperature to the allowed value, and then the cooling water enters the condenser again making cycle utilizing. Since the system water level is basically stable, the lift of the cycling pump is still stable and its capacity is determined according to the computed water flow.
The cycling pump operates continuously for long time along with the generator unit. Since the load of the generator unit varies frequently, it is required to adjust the cycling water flow to ensure safe and economic operation of the generator unit. Even with the same load, different external environment makes the requirements for the cycling water different. According to the present condition - the flow for one pump is not enough and the flow for two pumps is too high as well as the outlet valve cannot be adjusted, one cycling pump may satisfy the operating requirements in all day of winter, after midnight in spring and operating mode of low load. The operating time of the cycling pump is computed according to 200 days averagely and 150 days for two cycling pumps. When the cycling pump operates with full load, the operating current of the motor is 195A.
It is necessary to adjust the flow according to the operating mode by using variable speed drive. Based on the practical requirement, the speed of the motor of cycling pumps is adjusted through variable speed drive. Since the nature of the pumps, speed adjustment may adjust the pump flow and the power consumption of the motor may also be reduced, then, the purpose to control for the most beneficial vacuum can be achieved. Thus the technology will be improved, power consumption will be decreased and energy saving will be obtained.
Economic Operation of Turbines and Control of Cycling Pump Flow
At present, the vacuum of turbines is mainly controlled by means of adjusting cooling water flow. It is known from the operation principle of turbines that the pressure in condensers in operation mainly depends on the steam load, temperature at cooling water inlet and cooling water flow. The temperature of cooling water usually depends on natural condition. Under the condition of certain steam load, the vacuum of condensers may only be improved by increasing the cooling water flow. To improve economy of operation of the generator unit,the turbine power increment for increasing of vacuum ΔΝ1 should be greater than the consumed power for increasing the cycling water flow ΔΝ2. Obviously, The most beneficial vacuum of turbines Peco (economic vacuum) should be located at the maximum of net increased powerΔΝ=ΔΝ2 -ΔΝ1. At this position, the turbine operates in the economic operation mode, as shown in Fig 1:
Fig.1 The turbine's most beneficial vacuum confirmation
In the figure, Dw is cooling water flow, P is vacuum in the condenser of turbines, ΔΝ is the power difference, and when the cooling water flow is rather small, ΔΝ increases as the cooling water flow increases, and it reaches maximum at point a. If the cooling water flow increases further, on the contrary ΔΝ will decrease until to zero. But at point c, the expandability of the turbine has reached the limit and the power of the turbine will not increase. The vacuum corresponding to point c becomes the limit vacuum. It may be known that drawing a equal flow line from point a, which crosses with the condenser pressure line at point b, the vacuum Peco corresponding to point b is the most beneficial vacuum. The cooling water flow Deco, corresponding to point a, is the best cooling water flow. Through determination of the most beneficial vacuum of the turbine and controlling the cooling water flow based on this, the exhaust pressure of the turbine is kept to the most beneficial vacuum to ensure that the generator unit is operating under the economic mode.
It may be seen from the above analysis that varying the cycling water flow may improve economy of operation of generator units.
Control Principle of Cycling Pumps at the Most Beneficial Vacuum of turbines
Implementation of the most beneficial vacuum depends on adjusting cycling water flow. The DCS of the generator unit controls the operating condition of the cycling pump, adjust the operating number of cycling pumps and speed, and control the cycling water flow to keep the turbine vacuum at the most beneficial vacuum, ensuring economic operation of the generator units. The speed adjusting of cycling pumps is the key for the most beneficial vacuum control system of turbines. Controlling the speed of cycling pumps through variable speed drive and the control mode is "one variation and one fix".
With multi-level cell-connection-in-series technology, medium voltage variable speed drive is composed of phase-shifting transformer, power cell and controller (For the configuration of the 6kV system, see Fig 2). The 6 kV series variable speed drive has 15 power cells and every 5 cells make up a phase in series.
All cells are identical in the structure and electrical parameters of and may be replaced each other. The circuit is basic AC-DC-AC single-phase variable speed drive circuit (See Fig 3). The rectifier is a three-phase diode bridge. Controlling the IGBT inverter by sinusoidal PWM way, the output voltage waveform is shown in fig 4.
Fig.2 Structure of medium voltage variable speed drive
Fig.3 Circuit of power cell
Fig. 4 PWM waveform of the cell output
Each secondary of the phase shifting transformer supplies power to a power cell. The transformer's secondaries are divided into three groups. For 6000V series, 42 pulses rectifier mode is formed. The multi-pulse overlap rectifier mode greatly improves the quality of the line current waveform, and the input power factor can be improved up to near 1.
In addition, the independence of the transformer's secondaries makes the power cells' main circuit relatively separate. The main circuit of the power cell is similar to the circuit of the low voltage variable speed drive.
At the output side, each cell's U terminal and the neighbor cell's V terminal are connected in series to form a three phase star (wye) connection to supply power for the motor. By overlapping each cell's PWM waveform, we can get the multi-level SPWM waveform shown in Fig. 5. It is a excellent sine-shape, small dv/dt, no cable and motor insulation destruction, no output filter for long output cable, no motor derating, and it can be used in driving the old motor directly. Meanwhile the motor harmonics are reduced greatly, the mechanical vibration is eliminated, and the mechanical stress of shaft and vanes is reduced.
When one cell fails, this cell may be bypassed off the system through making the soft switch node K in Fig. 3 short and the operation of other cells will not be affected. In this cases, medium voltage variable speed drive operates with derating, the loss resulted from variable speed drive's stop in many cases may be avoided.
Fig. 5 Step PWM waveform of medium voltage variable speed drive output phase voltage
Two cycling pumps are provided with the generator unit #1. One of the cycling pumps is added with variable speed drive to perform speed control. The related parameters of the cycling pump are as follows:
Model: Inclined flow pump, Stand type, 1600B
Flow: Q=18,500 m3/h
Lift: H=18.2m
Rated speed: 370RPM
Driving motor: YL1800-16
Driving power: 1,800kW
Rated current: 223A
Rated speed: 375RPM
The technical parameters of the variable speed drive are shown in the following table:
In order to fully ensure the system reliability, a bypass device is configured with the medium voltage variable speed drive. When the medium voltage variable speed drive operates abnormally, it will stop and the motor may be manually switched to be driven directly by the power supply. The bypass circuit is composed of 3 medium voltage disconnect switches QS1, QS2 and QS3 (see the fig.6 in which QF is the original medium voltage switch). It is required that QS2 and QS3 may not be closed simultaneously and they are interlocked mechanically. When the motor is driven by medium voltage variable speed drive, QS1 and QS2 are closed and QS3 is open; and when the motor is driven by the power, QS3 is closed and QS1 and QS2 are open.
Fig.6 bypass circuit
In order to protect from medium voltage variable speed drive failure, the variable speed drive is interlocked with the 6kV switch QF. Once medium voltage variable speed drive fails, medium voltage variable speed drive will make QF switched off. It is required that the user makes suitable reform to the switching circuit. When the bypass circuit is acted, medium voltage variable speed drive will allow QF switch-on and cancel the switch off signal to enable the motor to start with the power through QF switching on.
To ensure safe operation of the generator unit, the reserved cycling pump is required to operate automatically under the operation mode of single cycling pump with variable speed drive, when variable speed drive fails and QF switches off. To adapt the improvement of automation level of cycling pump system after reform with variable speed drive, the outlet water valve is also interlocked for automatic control. The function of the valve interlock is: During the pump starts and its speed increases, the pump outlet water pressure increases gradually, and when the pressure is greater than the "minimum outlet water pressure for opening valve", the valve begins to open until to open fully. When the pump stops, the valve will close simultaneously. If the valve opens not completely for various reasons when the pump starts, "valve not open fully" will be displayed. If the valve closes not completely when the pump stops, "valve not close fully" will be displayed. Thus, during starting and stopping the pump, the personnel on duty need not to perform any operation to the valve and thus, not only operation miss will decrease but also the shock to the pipe network during opening valve and closing valve will be very small.
The variable speed drive system is included in the present DCS system of the generator unit. Based on the load for the generator unit, DCS automatically control the speed of the driving motor of boiler cycling pump according to the setting program. The variable speed drive digital outputs needed to provide to DCS include: failure alarming (transformer temperature alarming, failure of cell cabinet fans, control power supply breaking off, controller failure, cell failure, analog signal breaking off), standby indication, operation indication, medium-voltage switch-on allowance, medium-voltage emerging switching off, opening valve (used when variable speed drive controls valve, i.e. open outlet butterfly valve), closing valve (used when variable speed drive controls valve, i.e. close outlet butterfly valve). The variable speed drive digital inputs to be provided by DCS include: starting variable speed drive (dry node, effective when closed, make variable speed drive start to operate), stopping variable speed drive (dry node, effective when closed, make variable speed drive stop normally), closing valve fully (dry node, effective when opened, show that the outlet butterfly valve of the pump controlled by variable speed drive has been closed fully), opening valve fully (dry node, effective when opened, show that the outlet butterfly valve of the pump controlled by variable speed drive has been opened fully). The variable speed drive analog inputs needed to be provided by DCS include: 1 channel of 4~20mA current source output, as the given speed of variable speed drive, i.e. the needed operating speed of the motor. The variable speed drive analog outputs needed to provide to DCS include: 2 channel of 4~20mA current source output, the physical variables corresponding to the analog output are output frequency and output current. The analog variables provided to variable speed drive at site include: 1 channel of 4~20mA current source output, representing the outlet pressure of the variable speed drive controlled pump for use when valves interlocked. The digital variables provided to variable speed drive by the medium-voltage switch cabinet include: 1 variable, medium-voltage switch has switched off. Closed node represents medium-voltage switch is at off position. The node will open when medium-voltage switch switches on.
The speed of cycling pumps is adjusted by operating personnel. The outputs of DCS are adjusted through the analog operating devices on the CRT of DCS system, referring to vacuum in the condenser and external temperature. These output are standard signals of 4~20mA feedback to variable speed drive. Corresponding to different given value of frequency (speed), variable speed drive adjusts the motor speed automatically through comparing speed output with given speed of DCS, implementing speed control of the cycling pump, thus reach the purpose of adjusting the water flow.
Based on these, by accumulating for a period of time, the given values under different load and temperature may be drawn into curves and determine the upper and lower limit of safety, formulating special algorithm for adjusting speed of cycling pumps. Meanwhile, using primary thermal measuring elements, the collected varying values of the load and temperature parameters may be sent to the DCS system of generator units. In the DCS system of generator units, control computation is performed and the computing results will form the command signals of given speed of 4~20 mA and the signal will feedback to variable speed drive. Through comparing speed output with given speed of DCS, variable speed drive adjusts the motor speed automatically, implementing speed control of the cycling pump.
Since this reform is for one of the two cycling pumps in parallel and under normal operating mode, one operates with the power supply and the other one operates with variable speed drive. Since the temperature difference between seasons as well as day and night, operation of variable speed drive system has its specificity. The outlet pressure of the pipe network depends on individual outlet pressure of the two cycling pumps in parallel and it determines that the pump with variable speed drive is not possible to operate with too low frequency, otherwise, flow back or no flow will happen. On the other hand, too low frequency will lead to the total pressure decreasing and the total lift requirement of the cycling system may not be satisfied. The pump operating with power supply and the fixed speed may also lead to over flow. Based the previous practical operating experience, under the condition that the pump operating with power supply and the pump operating with variable speed drive operate simultaneously, the lowest frequency for the pump with variable speed drive should be kept at greater than 38HZ. When the pump operating with variable speed drive operates by itself, the frequency for the pump with variable speed drive may be adjusted in the range of 5-45HZ as required (adjustment of frequency for the pump with variable speed drive must satisfy the lowest requirement for the outlet pressure of the cycling pump). The operating requirement may then be satisfied and the water flow may be adjusted continuously.
Contrast of the Test data for variable speed drive
The practical test results of the related parameters:
Table 1 Contrast of comprehensive input power for the pump operating with power supply and the pump operating with variable speed drive
The test results shown that the energy saving rate for 50% load is 60% and the energy saving rate for full load is also up to 20%
Based on the pump speed adjustment principle, when the driving motor of pumps operates with power supply, the output is the rated output, the speed and power consumption are rated value. When the driving motor of pumps operates with variable speed drive, the motor speed may be increased or decreased as required to vary the characteristic curve of the pump and make the rated parameters of the pump to satisfy the technology requirements. Based on the similar law of pumps, the relation between flow, lift, power and speed before and after application of variable speed drive is:
Q1/Q2= n1/n2
H1/H2= (n1/n2)2
P1/P2= (n1/n2)3
Q1, H1, P1 - Flow, lift, power of cycling pump at speed of n1;
Q2, H2, P2 - Flow, lift, power of cycling pump at speed of n2 and under similar operating mode.
Figure 7 Characteristic curve for cycling pump with variable speed drive
If speed decreases 50%, i.e., n2/n1=1/2, then P2/P1=1/8. It is clear that decreasing speed can reduce the power considerably and save energy. The above figure shows that when the speed decreases to n2 from n1, the rated parameters Q, H and P of the pump decrease. From the efficiency curve η- Q, the efficiency at point Q2 is same as the efficiency at point Q1 basically. That is to say when the speed decreases, rated operating parameters decrease correspondingly, but the efficiency does not decrease and increases even sometime. Therefore, under the prerequisite of satisfying operating requirements, the pump can still operate with same efficiency, or even higher.
The energy saving computation is as follows:
The operating time of the generator unit for the whole year is computed at 7,200 hours, in which the operating time for operating with double pumps and the operating time for operating with single pump are half of this time each. The operating time for operating with full load, 80% load, 70% load and 50% load are 1800 hours respectively. The electricity costs are 0.2 CNY/KWh.
Conclusion
Variable speed drive has saved the energy obviously. After using variable speed drive, soft starting for motors has been performed, motor life has been extended and vibration and wearing of pipes has been reduced. In brief, the application of variable speed drive in the speed adjusting reform for the cycling pump system of generator unit #1 in the Power Generation is quite successful. The advance and reliability of this series of variable speed drive has been verified by many industrial applications. In electrical power industry, popularizing and applying variable speed drive to many medium-voltage large-power accessory equipments can save energy a lot and is an effective way for reducing power consumption and saving energy. It has gained the supports from national industrial policy and represents the direction of energy saving and technical reform of electrical power industry. At present, more and more personnel in electrical power industry have formed common view for this.
Features of Operating Mode of Cycling Pumps
Closed cycling water systems are used for the generator unit and water supply systems of unit system are used for the cycling pumps, i.e. each generator is provided with one cooling tower, one pressure cycling water pipe, one gole with double holes and two cycling pumps, and under normal operating mode, two cycling pumps are operated for each generator unit. In the cycling water systems, cycle utilization of water resources is implemented by using the cycling pump. The hot water passes the heat exchanger and enters into the cooling facilities to cool down, reducing the water temperature to the allowed value, and then the cooling water enters the condenser again making cycle utilizing. Since the system water level is basically stable, the lift of the cycling pump is still stable and its capacity is determined according to the computed water flow.
The cycling pump operates continuously for long time along with the generator unit. Since the load of the generator unit varies frequently, it is required to adjust the cycling water flow to ensure safe and economic operation of the generator unit. Even with the same load, different external environment makes the requirements for the cycling water different. According to the present condition - the flow for one pump is not enough and the flow for two pumps is too high as well as the outlet valve cannot be adjusted, one cycling pump may satisfy the operating requirements in all day of winter, after midnight in spring and operating mode of low load. The operating time of the cycling pump is computed according to 200 days averagely and 150 days for two cycling pumps. When the cycling pump operates with full load, the operating current of the motor is 195A.
It is necessary to adjust the flow according to the operating mode by using variable speed drive. Based on the practical requirement, the speed of the motor of cycling pumps is adjusted through variable speed drive. Since the nature of the pumps, speed adjustment may adjust the pump flow and the power consumption of the motor may also be reduced, then, the purpose to control for the most beneficial vacuum can be achieved. Thus the technology will be improved, power consumption will be decreased and energy saving will be obtained.
Economic Operation of Turbines and Control of Cycling Pump Flow
At present, the vacuum of turbines is mainly controlled by means of adjusting cooling water flow. It is known from the operation principle of turbines that the pressure in condensers in operation mainly depends on the steam load, temperature at cooling water inlet and cooling water flow. The temperature of cooling water usually depends on natural condition. Under the condition of certain steam load, the vacuum of condensers may only be improved by increasing the cooling water flow. To improve economy of operation of the generator unit,the turbine power increment for increasing of vacuum ΔΝ1 should be greater than the consumed power for increasing the cycling water flow ΔΝ2. Obviously, The most beneficial vacuum of turbines Peco (economic vacuum) should be located at the maximum of net increased powerΔΝ=ΔΝ2 -ΔΝ1. At this position, the turbine operates in the economic operation mode, as shown in Fig 1:
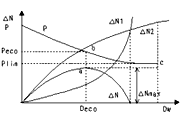
Fig.1 The turbine's most beneficial vacuum confirmation
In the figure, Dw is cooling water flow, P is vacuum in the condenser of turbines, ΔΝ is the power difference, and when the cooling water flow is rather small, ΔΝ increases as the cooling water flow increases, and it reaches maximum at point a. If the cooling water flow increases further, on the contrary ΔΝ will decrease until to zero. But at point c, the expandability of the turbine has reached the limit and the power of the turbine will not increase. The vacuum corresponding to point c becomes the limit vacuum. It may be known that drawing a equal flow line from point a, which crosses with the condenser pressure line at point b, the vacuum Peco corresponding to point b is the most beneficial vacuum. The cooling water flow Deco, corresponding to point a, is the best cooling water flow. Through determination of the most beneficial vacuum of the turbine and controlling the cooling water flow based on this, the exhaust pressure of the turbine is kept to the most beneficial vacuum to ensure that the generator unit is operating under the economic mode.
It may be seen from the above analysis that varying the cycling water flow may improve economy of operation of generator units.
Control Principle of Cycling Pumps at the Most Beneficial Vacuum of turbines
Implementation of the most beneficial vacuum depends on adjusting cycling water flow. The DCS of the generator unit controls the operating condition of the cycling pump, adjust the operating number of cycling pumps and speed, and control the cycling water flow to keep the turbine vacuum at the most beneficial vacuum, ensuring economic operation of the generator units. The speed adjusting of cycling pumps is the key for the most beneficial vacuum control system of turbines. Controlling the speed of cycling pumps through variable speed drive and the control mode is "one variation and one fix".
Principle of variable speed drives
With multi-level cell-connection-in-series technology, medium voltage variable speed drive is composed of phase-shifting transformer, power cell and controller (For the configuration of the 6kV system, see Fig 2). The 6 kV series variable speed drive has 15 power cells and every 5 cells make up a phase in series.
All cells are identical in the structure and electrical parameters of and may be replaced each other. The circuit is basic AC-DC-AC single-phase variable speed drive circuit (See Fig 3). The rectifier is a three-phase diode bridge. Controlling the IGBT inverter by sinusoidal PWM way, the output voltage waveform is shown in fig 4.
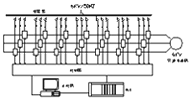
Fig.2 Structure of medium voltage variable speed drive
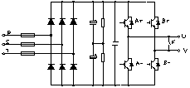
Fig.3 Circuit of power cell
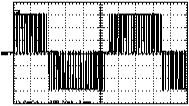
Fig. 4 PWM waveform of the cell output
Each secondary of the phase shifting transformer supplies power to a power cell. The transformer's secondaries are divided into three groups. For 6000V series, 42 pulses rectifier mode is formed. The multi-pulse overlap rectifier mode greatly improves the quality of the line current waveform, and the input power factor can be improved up to near 1.
In addition, the independence of the transformer's secondaries makes the power cells' main circuit relatively separate. The main circuit of the power cell is similar to the circuit of the low voltage variable speed drive.
At the output side, each cell's U terminal and the neighbor cell's V terminal are connected in series to form a three phase star (wye) connection to supply power for the motor. By overlapping each cell's PWM waveform, we can get the multi-level SPWM waveform shown in Fig. 5. It is a excellent sine-shape, small dv/dt, no cable and motor insulation destruction, no output filter for long output cable, no motor derating, and it can be used in driving the old motor directly. Meanwhile the motor harmonics are reduced greatly, the mechanical vibration is eliminated, and the mechanical stress of shaft and vanes is reduced.
When one cell fails, this cell may be bypassed off the system through making the soft switch node K in Fig. 3 short and the operation of other cells will not be affected. In this cases, medium voltage variable speed drive operates with derating, the loss resulted from variable speed drive's stop in many cases may be avoided.
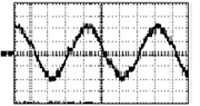
Fig. 5 Step PWM waveform of medium voltage variable speed drive output phase voltage
Variable speed drive Reform Scheme
Two cycling pumps are provided with the generator unit #1. One of the cycling pumps is added with variable speed drive to perform speed control. The related parameters of the cycling pump are as follows:
Model: Inclined flow pump, Stand type, 1600B
Flow: Q=18,500 m3/h
Lift: H=18.2m
Rated speed: 370RPM
Driving motor: YL1800-16
Driving power: 1,800kW
Rated current: 223A
Rated speed: 375RPM
The technical parameters of the variable speed drive are shown in the following table:
Applied standard | Q/HD BLH004-2001 |
Model | Gozuk-220 |
Site of installation | In door |
Technical style | Power modules cascaded,AC-DC-AC, high voltage in high voltage out |
Motor | Common squirrel-cage asynchronism |
Fuse on variable speed drive input | Without fuse on variable speed drive input |
Rated input voltage and range | 6kV±10% |
System input voltage | 6kV±10% |
System output voltage | 0~6kV |
System output current | 220 A |
Inverter Max. output voltage | 6 kV |
Rated capacity | 2250kVA |
Rated input frequency and range | 50Hz±10% |
Sensitivity to line voltage fluctuation | +15%~-30% |
variable speed drive efficiency | >0.96 |
Harmony | Input current<4%, output voltage<6%,output current<2% |
Input line power factor | >0.95 (20%load) |
Control mode | Multi-level sinusoid PWM control |
Motor inverter mode | IGBT inverter bridge connection |
Rectifier | 30 pulse, three phase diode bridge |
Drive quadrant | 1 quadrant (2 quadrant optional) |
Whether fiber optic are applied to the electricity isolation | Adopt HP HFBR-EUS100 fiber optic |
Noise | ≤75dB |
Cooling method | Forced air cooling |
Overload capacity | 120% 1min, 150% 3s,200%prompt protection (<10μs) |
Standard control connection | RS485 |
Protection class | ≥IP20 |
Operating keypad | Chinese color touchable LCD |
User interface language | Simple Chinese |
In order to fully ensure the system reliability, a bypass device is configured with the medium voltage variable speed drive. When the medium voltage variable speed drive operates abnormally, it will stop and the motor may be manually switched to be driven directly by the power supply. The bypass circuit is composed of 3 medium voltage disconnect switches QS1, QS2 and QS3 (see the fig.6 in which QF is the original medium voltage switch). It is required that QS2 and QS3 may not be closed simultaneously and they are interlocked mechanically. When the motor is driven by medium voltage variable speed drive, QS1 and QS2 are closed and QS3 is open; and when the motor is driven by the power, QS3 is closed and QS1 and QS2 are open.
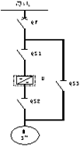
Fig.6 bypass circuit
In order to protect from medium voltage variable speed drive failure, the variable speed drive is interlocked with the 6kV switch QF. Once medium voltage variable speed drive fails, medium voltage variable speed drive will make QF switched off. It is required that the user makes suitable reform to the switching circuit. When the bypass circuit is acted, medium voltage variable speed drive will allow QF switch-on and cancel the switch off signal to enable the motor to start with the power through QF switching on.
To ensure safe operation of the generator unit, the reserved cycling pump is required to operate automatically under the operation mode of single cycling pump with variable speed drive, when variable speed drive fails and QF switches off. To adapt the improvement of automation level of cycling pump system after reform with variable speed drive, the outlet water valve is also interlocked for automatic control. The function of the valve interlock is: During the pump starts and its speed increases, the pump outlet water pressure increases gradually, and when the pressure is greater than the "minimum outlet water pressure for opening valve", the valve begins to open until to open fully. When the pump stops, the valve will close simultaneously. If the valve opens not completely for various reasons when the pump starts, "valve not open fully" will be displayed. If the valve closes not completely when the pump stops, "valve not close fully" will be displayed. Thus, during starting and stopping the pump, the personnel on duty need not to perform any operation to the valve and thus, not only operation miss will decrease but also the shock to the pipe network during opening valve and closing valve will be very small.
The variable speed drive system is included in the present DCS system of the generator unit. Based on the load for the generator unit, DCS automatically control the speed of the driving motor of boiler cycling pump according to the setting program. The variable speed drive digital outputs needed to provide to DCS include: failure alarming (transformer temperature alarming, failure of cell cabinet fans, control power supply breaking off, controller failure, cell failure, analog signal breaking off), standby indication, operation indication, medium-voltage switch-on allowance, medium-voltage emerging switching off, opening valve (used when variable speed drive controls valve, i.e. open outlet butterfly valve), closing valve (used when variable speed drive controls valve, i.e. close outlet butterfly valve). The variable speed drive digital inputs to be provided by DCS include: starting variable speed drive (dry node, effective when closed, make variable speed drive start to operate), stopping variable speed drive (dry node, effective when closed, make variable speed drive stop normally), closing valve fully (dry node, effective when opened, show that the outlet butterfly valve of the pump controlled by variable speed drive has been closed fully), opening valve fully (dry node, effective when opened, show that the outlet butterfly valve of the pump controlled by variable speed drive has been opened fully). The variable speed drive analog inputs needed to be provided by DCS include: 1 channel of 4~20mA current source output, as the given speed of variable speed drive, i.e. the needed operating speed of the motor. The variable speed drive analog outputs needed to provide to DCS include: 2 channel of 4~20mA current source output, the physical variables corresponding to the analog output are output frequency and output current. The analog variables provided to variable speed drive at site include: 1 channel of 4~20mA current source output, representing the outlet pressure of the variable speed drive controlled pump for use when valves interlocked. The digital variables provided to variable speed drive by the medium-voltage switch cabinet include: 1 variable, medium-voltage switch has switched off. Closed node represents medium-voltage switch is at off position. The node will open when medium-voltage switch switches on.
The speed of cycling pumps is adjusted by operating personnel. The outputs of DCS are adjusted through the analog operating devices on the CRT of DCS system, referring to vacuum in the condenser and external temperature. These output are standard signals of 4~20mA feedback to variable speed drive. Corresponding to different given value of frequency (speed), variable speed drive adjusts the motor speed automatically through comparing speed output with given speed of DCS, implementing speed control of the cycling pump, thus reach the purpose of adjusting the water flow.
Based on these, by accumulating for a period of time, the given values under different load and temperature may be drawn into curves and determine the upper and lower limit of safety, formulating special algorithm for adjusting speed of cycling pumps. Meanwhile, using primary thermal measuring elements, the collected varying values of the load and temperature parameters may be sent to the DCS system of generator units. In the DCS system of generator units, control computation is performed and the computing results will form the command signals of given speed of 4~20 mA and the signal will feedback to variable speed drive. Through comparing speed output with given speed of DCS, variable speed drive adjusts the motor speed automatically, implementing speed control of the cycling pump.
Since this reform is for one of the two cycling pumps in parallel and under normal operating mode, one operates with the power supply and the other one operates with variable speed drive. Since the temperature difference between seasons as well as day and night, operation of variable speed drive system has its specificity. The outlet pressure of the pipe network depends on individual outlet pressure of the two cycling pumps in parallel and it determines that the pump with variable speed drive is not possible to operate with too low frequency, otherwise, flow back or no flow will happen. On the other hand, too low frequency will lead to the total pressure decreasing and the total lift requirement of the cycling system may not be satisfied. The pump operating with power supply and the fixed speed may also lead to over flow. Based the previous practical operating experience, under the condition that the pump operating with power supply and the pump operating with variable speed drive operate simultaneously, the lowest frequency for the pump with variable speed drive should be kept at greater than 38HZ. When the pump operating with variable speed drive operates by itself, the frequency for the pump with variable speed drive may be adjusted in the range of 5-45HZ as required (adjustment of frequency for the pump with variable speed drive must satisfy the lowest requirement for the outlet pressure of the cycling pump). The operating requirement may then be satisfied and the water flow may be adjusted continuously.
Contrast of the Test data for variable speed drive
The practical test results of the related parameters:
Table 1 Contrast of comprehensive input power for the pump operating with power supply and the pump operating with variable speed drive
Load for generator unit (MW) |
Frequency/current before reform | Frequency/current after reform | Reduced volume of comprehensive input power (kW) |
1500 | 50Hz/195A | 38Hz/78.00A | 997 |
2100 | 50Hz/195A | 40Hz/85.00A | 937 |
2400 | 50Hz/195A | 44.87Hz/113.40A | 695 |
3000 | 50Hz/195A | 49.95Hz/155.55A | 336 |
The test results shown that the energy saving rate for 50% load is 60% and the energy saving rate for full load is also up to 20%
Benefits of variable speed drive after Reform
Based on the pump speed adjustment principle, when the driving motor of pumps operates with power supply, the output is the rated output, the speed and power consumption are rated value. When the driving motor of pumps operates with variable speed drive, the motor speed may be increased or decreased as required to vary the characteristic curve of the pump and make the rated parameters of the pump to satisfy the technology requirements. Based on the similar law of pumps, the relation between flow, lift, power and speed before and after application of variable speed drive is:
Q1/Q2= n1/n2
H1/H2= (n1/n2)2
P1/P2= (n1/n2)3
Q1, H1, P1 - Flow, lift, power of cycling pump at speed of n1;
Q2, H2, P2 - Flow, lift, power of cycling pump at speed of n2 and under similar operating mode.
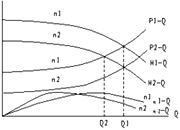
Figure 7 Characteristic curve for cycling pump with variable speed drive
If speed decreases 50%, i.e., n2/n1=1/2, then P2/P1=1/8. It is clear that decreasing speed can reduce the power considerably and save energy. The above figure shows that when the speed decreases to n2 from n1, the rated parameters Q, H and P of the pump decrease. From the efficiency curve η- Q, the efficiency at point Q2 is same as the efficiency at point Q1 basically. That is to say when the speed decreases, rated operating parameters decrease correspondingly, but the efficiency does not decrease and increases even sometime. Therefore, under the prerequisite of satisfying operating requirements, the pump can still operate with same efficiency, or even higher.
The energy saving computation is as follows:
The operating time of the generator unit for the whole year is computed at 7,200 hours, in which the operating time for operating with double pumps and the operating time for operating with single pump are half of this time each. The operating time for operating with full load, 80% load, 70% load and 50% load are 1800 hours respectively. The electricity costs are 0.2 CNY/KWh.
- When generator unit#1 operating with full load and double pumps, the estimated annual electricity savings is 302,400 KWh. Annual electricity cost savings is RMB60,480 at least.
- When generator unit#1 operating with full load and single pumps, the estimated annual electricity savings is 302,400 KWh. Annual electricity cost savings is RMB60,480 at least.
- When generator unit#1 operating with 80% load and double pumps, the estimated annual electricity savings is 625,500 KWh. Annual electricity cost savings is RMB125,100 at least.
- When generator unit#1 operating with 80% load and single pumps, the estimated annual electricity savings is 625,500 KWh. Annual electricity cost savings is RMB125,100 at least.
- When generator unit#1 operating with 70% load and double pumps, the estimated annual electricity savings is 843,300 KWh. Annual electricity cost savings is RMB168,660 at least.
- When generator unit#1 operating with 70% load and single pumps, the estimated annual electricity savings is 843,300 KWh. Annual electricity cost savings is RMB168,660 at least.
- When generator unit#1 operating with 50% load and double pumps, the estimated annual electricity savings is 897,300 KWh. Annual electricity cost savings is RMB179,460 at least.
- When generator unit#1 operating with 50% load and single pumps, the estimated annual electricity savings is 897,300 KWh. Annual electricity cost savings is RMB179,460 at least.
Conclusion
Variable speed drive has saved the energy obviously. After using variable speed drive, soft starting for motors has been performed, motor life has been extended and vibration and wearing of pipes has been reduced. In brief, the application of variable speed drive in the speed adjusting reform for the cycling pump system of generator unit #1 in the Power Generation is quite successful. The advance and reliability of this series of variable speed drive has been verified by many industrial applications. In electrical power industry, popularizing and applying variable speed drive to many medium-voltage large-power accessory equipments can save energy a lot and is an effective way for reducing power consumption and saving energy. It has gained the supports from national industrial policy and represents the direction of energy saving and technical reform of electrical power industry. At present, more and more personnel in electrical power industry have formed common view for this.
<- - I have an Opinion - ->