Variable speed drive for Condenser Pumps
Operating Mode of Condenser Pumps
The steam finished working in the turbine, will condense in the condenser, it is collected in the hot water well. The function of the condenser pump is to pump the condensed water into the deaerator in time. To keep the condenser pump operating continuously and stably is an important aspect for keeping the power plant operating safely and economically.
Monitoring and adjusting water level in a condenser is a main work for the operation of condenser pump. Under normal operation condition, the water level in the condenser should not be too high or too low. When the load of the generator increases, the condensed water volume increases and the water level in the condenser rises correspondingly. When the load of the generator decreases, the water level in the condenser lowers correspondingly.
The motor for the condenser pump is 6KV/1000KW and it is designed certain margin. Each generator is equipped with two condenser pumps. One is operating and another one is reserved. Before using variable speed drive, the water level adjustment is performed through varying the opening of outlet valve of the condenser pump. The linearity of adjustment is low and a large amount of energy is lost in the valve. Meanwhile, frequent operation of the valve leads the reliability of the valve decreasing and the stability of the operation of the generator is affected.
After using variable speed drive, the outlet valve of the condenser pump basically needs not to be adjusted frequently and the valve opening is kept in a rather wide range. Motor speed is changed by varying the output frequency of the variable speed drive to adjust the outlet flow and satisfy the requirements for the operating mode.
The variable speed drive system is of voltage resource type and has features of stable operation, wide speed regulating range, good output waveform, low input current harmonic, high power factor and high effectiveness, etc. It has low harmonic contamination to the electric network. The total harmonic distortion THD is less than 4% and complies with the standard of harmonic suppression of IEEE519-1992 directly and input harmonic filters are not required to be used. It has high power factor and power factor correction capacitors are not required. It has good output waveform, without additional heating of motor, torque pulsing, noises, output dv/dt and common mode voltage, etc. caused by harmonic. Output filters are not necessary and common asynchronous motors can be used.
The variable speed drive uses topology structure of cells in series, multi-level PWM (in brief CSML). Direct high voltage output is implemented in the form of several low-voltage PWM variable frequency power cells in series. Optic fibers connections are used between the high-voltage main loop and the controller, safe and reliable. It has accurate failure alarming protection, with functions of electronic protection of electric power and industrial electrical protection to ensure the safety and reliability under normal operation and failure of variable speed drive and motors.
Power cells are supplied by power network of 6kV decreased by isolation transformers with multi-plied secondaries. Power cells are AC-DC-AC PWM voltage resource inverter structure with three-phase input and single-phase output. Output ends of power cells connect in series each other formed ‘Y' structure to fulfill variable speed drive's direct medium output feeded the medium motors. Every phase of 6kV output voltage is consisted of 7 power cells with 480V rated voltage connected in series. Its output phase voltage is 3450V and line voltage is around 6kV. Every cell is loaded with all the motor current but only put out 1/7 phase voltage and 1/21 power.
Each cell is powered by one group of the input transformer's secondaries. Power cells and transformer's secondaries insulate each other. The secondaries are connected in the way of extended sides triangle to fulfill multi-ply so as to decrease input harmonic current. Even the unbalanced current happened, the generally same current can be ensured to reach the ideal effect of harmony elimination. For the output voltage of 6kV, the 21 secondaries feed 21 power cells are divided into 3 groups and each group is consisted of 7 different phase with 60/7 degree electric angle difference to form 42 pulse rectifier circuit structure. The input current wave form is near sinusoidal and total harmony current distortion lower 4% and input power factor can reach above 0.95.
The inverter output adopts the multi-level shifting-phase PWM technology. The same phase power cells out put the basic wave voltage with the same magnitude and phase. But the wave load of each cell in series has some electric degree to fulfill multi-level PWM and the output voltage is almost sinusoidal waveform. Every level step of the output voltage is the same as cell DC mother line voltage so the value of dv/dt is small. The lower switch on-off frequency is applied to the power cell in order to decrease the wear of switches. Moreover the amount of output level is increased. 6kV output voltage out put 15 levels phase voltage and 29 levels line voltage and the equal output frequency is 9KHz, which is benefit to improve the output waveform, decrease output harmonics. So the motor overheating, noise and torque pulse etc. caused by harmonics are decreased deeply. And it can be used in driving the common asynchronous motor directly. The failure of the motor insulation caused by surge voltage increase because of walk wave reflection with long output cable will not happen.
It is the power cell connected in series not power components. It is unnecessary to connect components in series because the highest voltage the components beared comes from cell DC mother line. In this way, the even voltage caused by in series components is avoided. Using low voltage IGBT power modules, the components failure occurs not easily working under low voltage. 6kv variable speed drive uses 42 couples 1200v low voltage IGBT. The drive power of low voltage IGBT is lower and the circuit can be easily driven with low frequency of switch on or off. It is unnecessary to adopt even voltage circuit and surge absorption circuit and the system efficiency is high. At the same time the power cell is designed capacitance filter structure. In general, the variable speed drive technology is matured and reliable.
Variable speed drive can bear 30% drop of voltage and continues to operate. When the main power supply of 6KV of variable speed drive is out of power completely, it may continue to operate for 3 seconds, thus to satisfy the requirements of continuous operation of variable speed drive, when the power lines of the variable speed drive switches. In addition, when the main power supply of 6KV is low voltage, the variable speed drive will continue to operate with derated voltage and recover to the original speed when the voltage becomes normal.
Uncontrolled diode rectifying circuits are used to the variable speed drive. variable speed drive can bear the surge voltage better. The surge voltage caused by thundering or switching will pass through the transformers (the impedance of a transformer is 8% usually) to produce surge current. And then the surge current will charge the filtering capacitors through the rectifying diodes of the power cells, and the filtering capacitors can fully absorb the surge energy that has entered into the cells. In addition, surge absorbing devices of pressure sensitive resistors, which are set at the primary side of the transformer have a protective function.
Power cells adapt module structure. All the power cells in the same variable speed drive are completely identical in structure and are exchangeable. It is very easy for maintenance. And only remove 3 AC input terminals, 2 AC output terminals as well as 1 optic fiber plug, will the power cells be drawn out. When one power module fails, the user may replace with a reserved power module through simple operation in 5 minutes to ensure the reliable system operation. All power modules have two indicator lights, one for indication of live status and the other for indication of operation. The operation condition of the module can be known clearly.
Power cells are multi-level modules in series. When one module fails, it will be bypassed automatically to enable to take corresponding measures at site. A parallel bypass circuit is connected between the output terminals of each power cell. When the power cell fails, the triggering signal for the corresponding power cell IGBT will be locked and make the bypass SCR short, forming a channel for the motor current to pass. When bypassing the failed power cell, two other corresponding power cells for the other two phases are also bypassed at the same time to ensure the symmetry of the three-phase voltage. For the variable speed drive of 6KV, each phase has 7 power cells in series, when one cell has been bypassed for each phase, the other 6 power cells will be left to operate for each phase, and their highest output voltage will be 86% of the rated voltage, the output current up to 100% as well as the output power up to about 86%. The loaded pump speed may still be more than 92%. The production requirement can be basically satisfied and the system operation reliability is increased greatly.
The input dry transformer is free of maintenance and has high reliability. The common protection of the transformer and the variable speed drive is a IP21 protective case, which may prevent the entering of external solid matter with a diameter of more than 12mm as well as mice, snakes, cats and sparrows, etc. from causing power failure for short circuit and provide safety guarantee for the live parts.
High speed adjusting accuracy, precise output frequency resolution (0.01Hz) and continuously adjustable output frequency 0.5Hz-120Hz can satisfy the operation mode requirements of production technology for generators. Soft starting, soft braking and automatic control of speed for motors can be performed. The starting current will be less than the rated current. The starting time of motors can be adjusted continuously, and the affects to the electric network will then be reduced.
Operating and monitoring software with self-owned, independent copyrights are preinstalled in variable speed drive and WINDOWS operating interfaces are used for local and remote starting and stopping, function setting, parameters setting and operation log inquiring etc.; With color screen of 12.1”, the setting function of complete and common variable speed drive parameters can be realized and the operation charts can be printed out; Adjusting the touching screen, voltage & current waveform, frequency and motor speed can be displayed at any time and the real-time status of motors at any time can be displayed visually; It has high diagnostic and indicating capability and can detect the operating conditions of various parts of the variable speed drive. It has complete failure monitoring circuits and precise failure locating capability. All the modules are of intellectual design. When failures occur, the failure information will be sent to the main control unit and the main control unit will switch off the main power cell IGBT in time, protecting the main circuit and displaying failure location and classification precisely on the Chinese human machine interface to see the failures at a glance. It is applicable to the skill level of ordinary operating and service personnel.
PLC is built in variable speed drive directly, thus the control logic is easy to modify, satisfying the requirements of the versatile site, and real seamless interface with the DCS system of generators can be implemented.
When external analog signals are used to control the output frequency of variable speed drive (the variable speed drive acts as the executive mechanism of DCS), variable speed drive can provide alarming signals and keep the original output frequency unchanged simultaneously, if break-off or short of analog signals occurs.
The control power supply of variable speed drive can accept AC 220V or DC 220V input and is equipped with UPS, which enables the system continue to operate when the control power supply fails and provide alarming simultaneously.
The steam finished working in the turbine, will condense in the condenser, it is collected in the hot water well. The function of the condenser pump is to pump the condensed water into the deaerator in time. To keep the condenser pump operating continuously and stably is an important aspect for keeping the power plant operating safely and economically.
Monitoring and adjusting water level in a condenser is a main work for the operation of condenser pump. Under normal operation condition, the water level in the condenser should not be too high or too low. When the load of the generator increases, the condensed water volume increases and the water level in the condenser rises correspondingly. When the load of the generator decreases, the water level in the condenser lowers correspondingly.
The motor for the condenser pump is 6KV/1000KW and it is designed certain margin. Each generator is equipped with two condenser pumps. One is operating and another one is reserved. Before using variable speed drive, the water level adjustment is performed through varying the opening of outlet valve of the condenser pump. The linearity of adjustment is low and a large amount of energy is lost in the valve. Meanwhile, frequent operation of the valve leads the reliability of the valve decreasing and the stability of the operation of the generator is affected.
After using variable speed drive, the outlet valve of the condenser pump basically needs not to be adjusted frequently and the valve opening is kept in a rather wide range. Motor speed is changed by varying the output frequency of the variable speed drive to adjust the outlet flow and satisfy the requirements for the operating mode.
Principle and features of Variable Speed Drives
The variable speed drive system is of voltage resource type and has features of stable operation, wide speed regulating range, good output waveform, low input current harmonic, high power factor and high effectiveness, etc. It has low harmonic contamination to the electric network. The total harmonic distortion THD is less than 4% and complies with the standard of harmonic suppression of IEEE519-1992 directly and input harmonic filters are not required to be used. It has high power factor and power factor correction capacitors are not required. It has good output waveform, without additional heating of motor, torque pulsing, noises, output dv/dt and common mode voltage, etc. caused by harmonic. Output filters are not necessary and common asynchronous motors can be used.
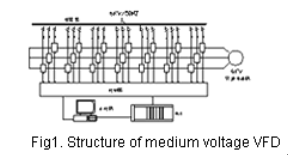
The variable speed drive uses topology structure of cells in series, multi-level PWM (in brief CSML). Direct high voltage output is implemented in the form of several low-voltage PWM variable frequency power cells in series. Optic fibers connections are used between the high-voltage main loop and the controller, safe and reliable. It has accurate failure alarming protection, with functions of electronic protection of electric power and industrial electrical protection to ensure the safety and reliability under normal operation and failure of variable speed drive and motors.
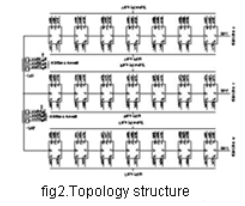
Power cells are supplied by power network of 6kV decreased by isolation transformers with multi-plied secondaries. Power cells are AC-DC-AC PWM voltage resource inverter structure with three-phase input and single-phase output. Output ends of power cells connect in series each other formed ‘Y' structure to fulfill variable speed drive's direct medium output feeded the medium motors. Every phase of 6kV output voltage is consisted of 7 power cells with 480V rated voltage connected in series. Its output phase voltage is 3450V and line voltage is around 6kV. Every cell is loaded with all the motor current but only put out 1/7 phase voltage and 1/21 power.
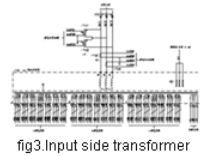
Each cell is powered by one group of the input transformer's secondaries. Power cells and transformer's secondaries insulate each other. The secondaries are connected in the way of extended sides triangle to fulfill multi-ply so as to decrease input harmonic current. Even the unbalanced current happened, the generally same current can be ensured to reach the ideal effect of harmony elimination. For the output voltage of 6kV, the 21 secondaries feed 21 power cells are divided into 3 groups and each group is consisted of 7 different phase with 60/7 degree electric angle difference to form 42 pulse rectifier circuit structure. The input current wave form is near sinusoidal and total harmony current distortion lower 4% and input power factor can reach above 0.95.
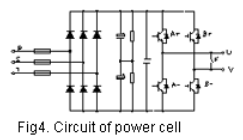
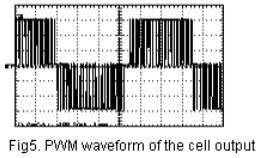
The inverter output adopts the multi-level shifting-phase PWM technology. The same phase power cells out put the basic wave voltage with the same magnitude and phase. But the wave load of each cell in series has some electric degree to fulfill multi-level PWM and the output voltage is almost sinusoidal waveform. Every level step of the output voltage is the same as cell DC mother line voltage so the value of dv/dt is small. The lower switch on-off frequency is applied to the power cell in order to decrease the wear of switches. Moreover the amount of output level is increased. 6kV output voltage out put 15 levels phase voltage and 29 levels line voltage and the equal output frequency is 9KHz, which is benefit to improve the output waveform, decrease output harmonics. So the motor overheating, noise and torque pulse etc. caused by harmonics are decreased deeply. And it can be used in driving the common asynchronous motor directly. The failure of the motor insulation caused by surge voltage increase because of walk wave reflection with long output cable will not happen.
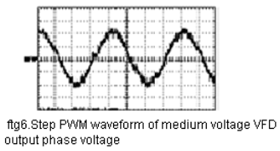
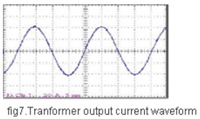
It is the power cell connected in series not power components. It is unnecessary to connect components in series because the highest voltage the components beared comes from cell DC mother line. In this way, the even voltage caused by in series components is avoided. Using low voltage IGBT power modules, the components failure occurs not easily working under low voltage. 6kv variable speed drive uses 42 couples 1200v low voltage IGBT. The drive power of low voltage IGBT is lower and the circuit can be easily driven with low frequency of switch on or off. It is unnecessary to adopt even voltage circuit and surge absorption circuit and the system efficiency is high. At the same time the power cell is designed capacitance filter structure. In general, the variable speed drive technology is matured and reliable.
Variable speed drive can bear 30% drop of voltage and continues to operate. When the main power supply of 6KV of variable speed drive is out of power completely, it may continue to operate for 3 seconds, thus to satisfy the requirements of continuous operation of variable speed drive, when the power lines of the variable speed drive switches. In addition, when the main power supply of 6KV is low voltage, the variable speed drive will continue to operate with derated voltage and recover to the original speed when the voltage becomes normal.
Uncontrolled diode rectifying circuits are used to the variable speed drive. variable speed drive can bear the surge voltage better. The surge voltage caused by thundering or switching will pass through the transformers (the impedance of a transformer is 8% usually) to produce surge current. And then the surge current will charge the filtering capacitors through the rectifying diodes of the power cells, and the filtering capacitors can fully absorb the surge energy that has entered into the cells. In addition, surge absorbing devices of pressure sensitive resistors, which are set at the primary side of the transformer have a protective function.
Power cells adapt module structure. All the power cells in the same variable speed drive are completely identical in structure and are exchangeable. It is very easy for maintenance. And only remove 3 AC input terminals, 2 AC output terminals as well as 1 optic fiber plug, will the power cells be drawn out. When one power module fails, the user may replace with a reserved power module through simple operation in 5 minutes to ensure the reliable system operation. All power modules have two indicator lights, one for indication of live status and the other for indication of operation. The operation condition of the module can be known clearly.
Power cells are multi-level modules in series. When one module fails, it will be bypassed automatically to enable to take corresponding measures at site. A parallel bypass circuit is connected between the output terminals of each power cell. When the power cell fails, the triggering signal for the corresponding power cell IGBT will be locked and make the bypass SCR short, forming a channel for the motor current to pass. When bypassing the failed power cell, two other corresponding power cells for the other two phases are also bypassed at the same time to ensure the symmetry of the three-phase voltage. For the variable speed drive of 6KV, each phase has 7 power cells in series, when one cell has been bypassed for each phase, the other 6 power cells will be left to operate for each phase, and their highest output voltage will be 86% of the rated voltage, the output current up to 100% as well as the output power up to about 86%. The loaded pump speed may still be more than 92%. The production requirement can be basically satisfied and the system operation reliability is increased greatly.
The input dry transformer is free of maintenance and has high reliability. The common protection of the transformer and the variable speed drive is a IP21 protective case, which may prevent the entering of external solid matter with a diameter of more than 12mm as well as mice, snakes, cats and sparrows, etc. from causing power failure for short circuit and provide safety guarantee for the live parts.
High speed adjusting accuracy, precise output frequency resolution (0.01Hz) and continuously adjustable output frequency 0.5Hz-120Hz can satisfy the operation mode requirements of production technology for generators. Soft starting, soft braking and automatic control of speed for motors can be performed. The starting current will be less than the rated current. The starting time of motors can be adjusted continuously, and the affects to the electric network will then be reduced.
Operating and monitoring software with self-owned, independent copyrights are preinstalled in variable speed drive and WINDOWS operating interfaces are used for local and remote starting and stopping, function setting, parameters setting and operation log inquiring etc.; With color screen of 12.1”, the setting function of complete and common variable speed drive parameters can be realized and the operation charts can be printed out; Adjusting the touching screen, voltage & current waveform, frequency and motor speed can be displayed at any time and the real-time status of motors at any time can be displayed visually; It has high diagnostic and indicating capability and can detect the operating conditions of various parts of the variable speed drive. It has complete failure monitoring circuits and precise failure locating capability. All the modules are of intellectual design. When failures occur, the failure information will be sent to the main control unit and the main control unit will switch off the main power cell IGBT in time, protecting the main circuit and displaying failure location and classification precisely on the Chinese human machine interface to see the failures at a glance. It is applicable to the skill level of ordinary operating and service personnel.
PLC is built in variable speed drive directly, thus the control logic is easy to modify, satisfying the requirements of the versatile site, and real seamless interface with the DCS system of generators can be implemented.
When external analog signals are used to control the output frequency of variable speed drive (the variable speed drive acts as the executive mechanism of DCS), variable speed drive can provide alarming signals and keep the original output frequency unchanged simultaneously, if break-off or short of analog signals occurs.
The control power supply of variable speed drive can accept AC 220V or DC 220V input and is equipped with UPS, which enables the system continue to operate when the control power supply fails and provide alarming simultaneously.
<- - I have an Opinion - ->