Variable speed drive fed motor from 50Hz to 60Hz
Variable speed drive shall be used where speed variation is a process requirement or it results in energy saving. This has to be decided based on application requirements. During my 24 year experience of designing variable speed drive motors for various applications all over the world I have come across very few users who simply use variable speed drive for fashion without knowing the implications. While designing variable speed drive motors one has to understand the applications to do full justice.
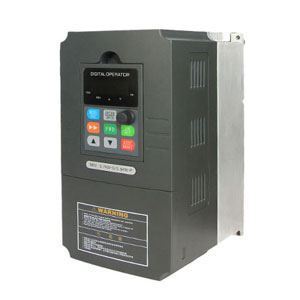
Most variable speed drive manufacturers require a reference to the neutral point of the winding, particularly for larger equipment. This connection serves as their primary "check" for unbalance in phase-phase and phase-ground circuits. As a side benefit, it keeps the VSD from accidentally damaging the machine winding insulation by over-voltaging the terminals by keeping the VSD and motor neutral at the same value.
The only way to obtain a neutral reference from the machine is to choose a wye (star) connection; the delta connection has no hard-wired neutral plane.
Smaller machines are often viewed as less sophisticated and/or less important to the overall process (commercial plug-and-play approach, if you will). This generally means less care is taken with getting the VSD and machine to match.
VSDs, because of their design, create harmonics in both current and voltage waveforms. Delta windings are not as good at dampening unwanted harmonics; they let all multiples of 3rd harmonic through. This can be significant, in terms of performance, as 3rd harmonic is often fairly high amplitude. (As a general statement, the higher the harmonic number, the lower the amplitude of the signal.)
The reason machines are designated star/delta start/run is an effort to reduce the inrush current of the equipment. A star-connected machine has line and phase currents equal; a delta-connected machine has line current = phase current * 1.732.
If your motor is 6 leads or more, it can operate at 415V 50 Hz. You can contact your motor supplier to make sure service factor will stay the same operating at 50Hz. Service factor tends to go down when operating at 50Hz due to increase of temperature rise inside the motor.
Lastly, "stock" motors are available for operation on variable speed drives from 50Hz to 60Hz. However, the general design is more robust for two reasons: first, it is more thermally forgiving (to handle the additional heating caused by VSD harmonics) and second, it has better strand and turn insulation in the winding (to combat the voltage spike resulting from the switching action used to create the waveform). These "stock" or "standard" variable speed drive designs are often designated as variable speed drive-capable. (If the manufacturer's catalog information does NOT indicate specifically that the equipment can be operated on a VSD, the safe route is to assume that it is not suitable - at least at the nameplate rating)
You can run across that frequency range easily as long as you maintain a constant volts per hertz ratio to keep the flux levels in the motor relatively constant, the strength constant and the heating constant. Most commercial inverters are great below line frequency, but they will not be able to supply the voltage to keep the V/Hz ratio constant. For example, 415V/50Hz=8.3 so X/85Hz=8.3 where X=706V. Unless it is being fed from a high voltage source, the inverter will not be able to put out 706 volts, so the motor will be weaker. There are vector control inverters out there that can compensate, but they are expensive.
Typical nominal point of operation of a wind power generator is slip=-10% (i.e. supersyncronous), which would mean in the case of 4-pole generator in 50 Hz grid a nominal speed of 1650 rpm. At slips close to zero (in other words rotor frequency close to zero), the speed of naturally 1500 rpm and the turbine operates at some partial power point, maybe 75 % of nominal power. So it is not a 'special' point for a wind turbine in any way. Note that below the synchronous speed the rotor frequency starts to increase from 50Hz to 60Hz again, so its maximums occur at the minimum and maximum speeds of the turbine. The converter is not modulating at lower speeds at all, since the DC-link voltage would be way too high. The converter contactor is closed somewhere between 900-1000 rpm in the example given above.
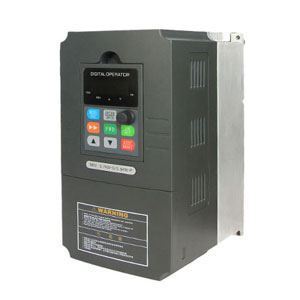
Most variable speed drive manufacturers require a reference to the neutral point of the winding, particularly for larger equipment. This connection serves as their primary "check" for unbalance in phase-phase and phase-ground circuits. As a side benefit, it keeps the VSD from accidentally damaging the machine winding insulation by over-voltaging the terminals by keeping the VSD and motor neutral at the same value.
The only way to obtain a neutral reference from the machine is to choose a wye (star) connection; the delta connection has no hard-wired neutral plane.
Smaller machines are often viewed as less sophisticated and/or less important to the overall process (commercial plug-and-play approach, if you will). This generally means less care is taken with getting the VSD and machine to match.
VSDs, because of their design, create harmonics in both current and voltage waveforms. Delta windings are not as good at dampening unwanted harmonics; they let all multiples of 3rd harmonic through. This can be significant, in terms of performance, as 3rd harmonic is often fairly high amplitude. (As a general statement, the higher the harmonic number, the lower the amplitude of the signal.)
The reason machines are designated star/delta start/run is an effort to reduce the inrush current of the equipment. A star-connected machine has line and phase currents equal; a delta-connected machine has line current = phase current * 1.732.
If your motor is 6 leads or more, it can operate at 415V 50 Hz. You can contact your motor supplier to make sure service factor will stay the same operating at 50Hz. Service factor tends to go down when operating at 50Hz due to increase of temperature rise inside the motor.
Lastly, "stock" motors are available for operation on variable speed drives from 50Hz to 60Hz. However, the general design is more robust for two reasons: first, it is more thermally forgiving (to handle the additional heating caused by VSD harmonics) and second, it has better strand and turn insulation in the winding (to combat the voltage spike resulting from the switching action used to create the waveform). These "stock" or "standard" variable speed drive designs are often designated as variable speed drive-capable. (If the manufacturer's catalog information does NOT indicate specifically that the equipment can be operated on a VSD, the safe route is to assume that it is not suitable - at least at the nameplate rating)
You can run across that frequency range easily as long as you maintain a constant volts per hertz ratio to keep the flux levels in the motor relatively constant, the strength constant and the heating constant. Most commercial inverters are great below line frequency, but they will not be able to supply the voltage to keep the V/Hz ratio constant. For example, 415V/50Hz=8.3 so X/85Hz=8.3 where X=706V. Unless it is being fed from a high voltage source, the inverter will not be able to put out 706 volts, so the motor will be weaker. There are vector control inverters out there that can compensate, but they are expensive.
Typical nominal point of operation of a wind power generator is slip=-10% (i.e. supersyncronous), which would mean in the case of 4-pole generator in 50 Hz grid a nominal speed of 1650 rpm. At slips close to zero (in other words rotor frequency close to zero), the speed of naturally 1500 rpm and the turbine operates at some partial power point, maybe 75 % of nominal power. So it is not a 'special' point for a wind turbine in any way. Note that below the synchronous speed the rotor frequency starts to increase from 50Hz to 60Hz again, so its maximums occur at the minimum and maximum speeds of the turbine. The converter is not modulating at lower speeds at all, since the DC-link voltage would be way too high. The converter contactor is closed somewhere between 900-1000 rpm in the example given above.
<- - I have an Opinion - ->